There are two sides to this coin, Random Inspection VS 100% Quality Inspection.Whether it is random inspection of each item or grouping inspection by quality. They all have different inspection methods. We will explain the differences between the two inspection methods and provide hints to help you improve efficiency.
What is Random Inspection?
Random inspection is a type of quality control that uses random sampling to inspect products. It is a statistical method for determining the quality of manufactured items by measuring their features, such as dimensions, weight and color. This technique allows manufacturers to reduce costs and improve fairness in product testing.
It is randomly implemented specifically so that manufacturers can’t plan ahead of the scheduled inspection and a more honest and clear view of the manufacturing processes are obvious to the inspector.
What is 100% Quality Inspection?
100% quality inspection is a type of quality control where each individual product is inspected in order to ensure they meet predetermined specifications. This method can be more time-consuming, expensive and less efficient than other types of quality inspection because it requires that every item be inspected by hand.
However, 100% quality inspection is often used in industries where safety is a concern. The process of inspecting every item can ensure that each product conforms to a certain standard of quality and safety. The inspection may be performed by humans or machines depending on the industry and type of product being produced.
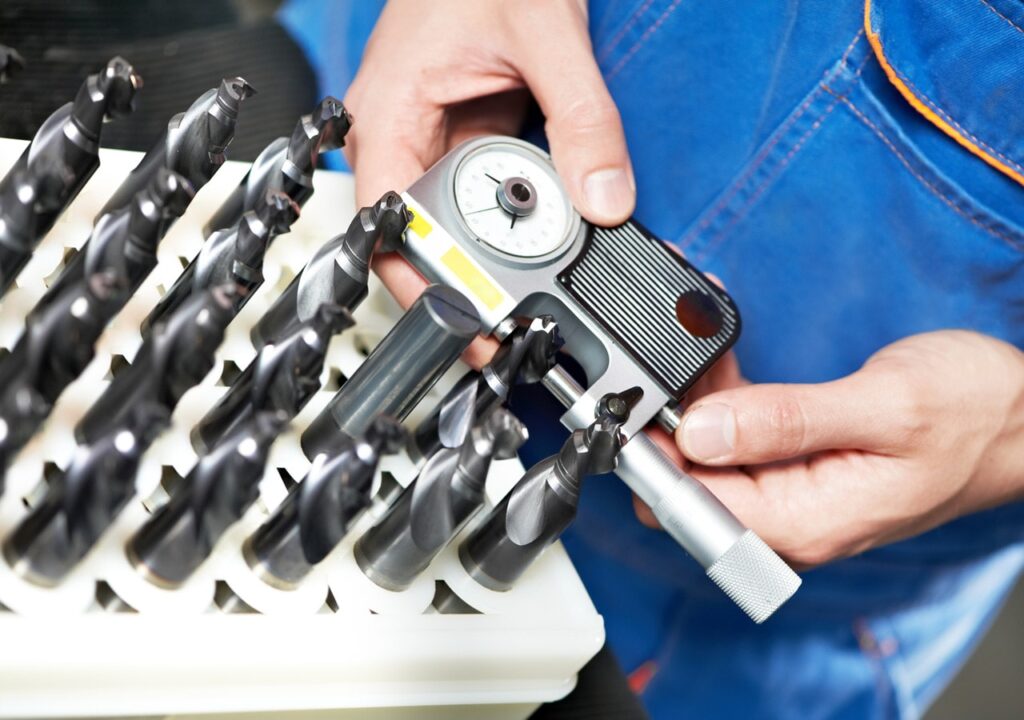
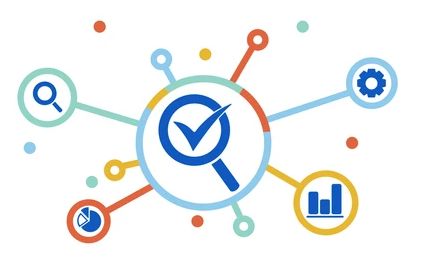
Advantages and disadvantages of both
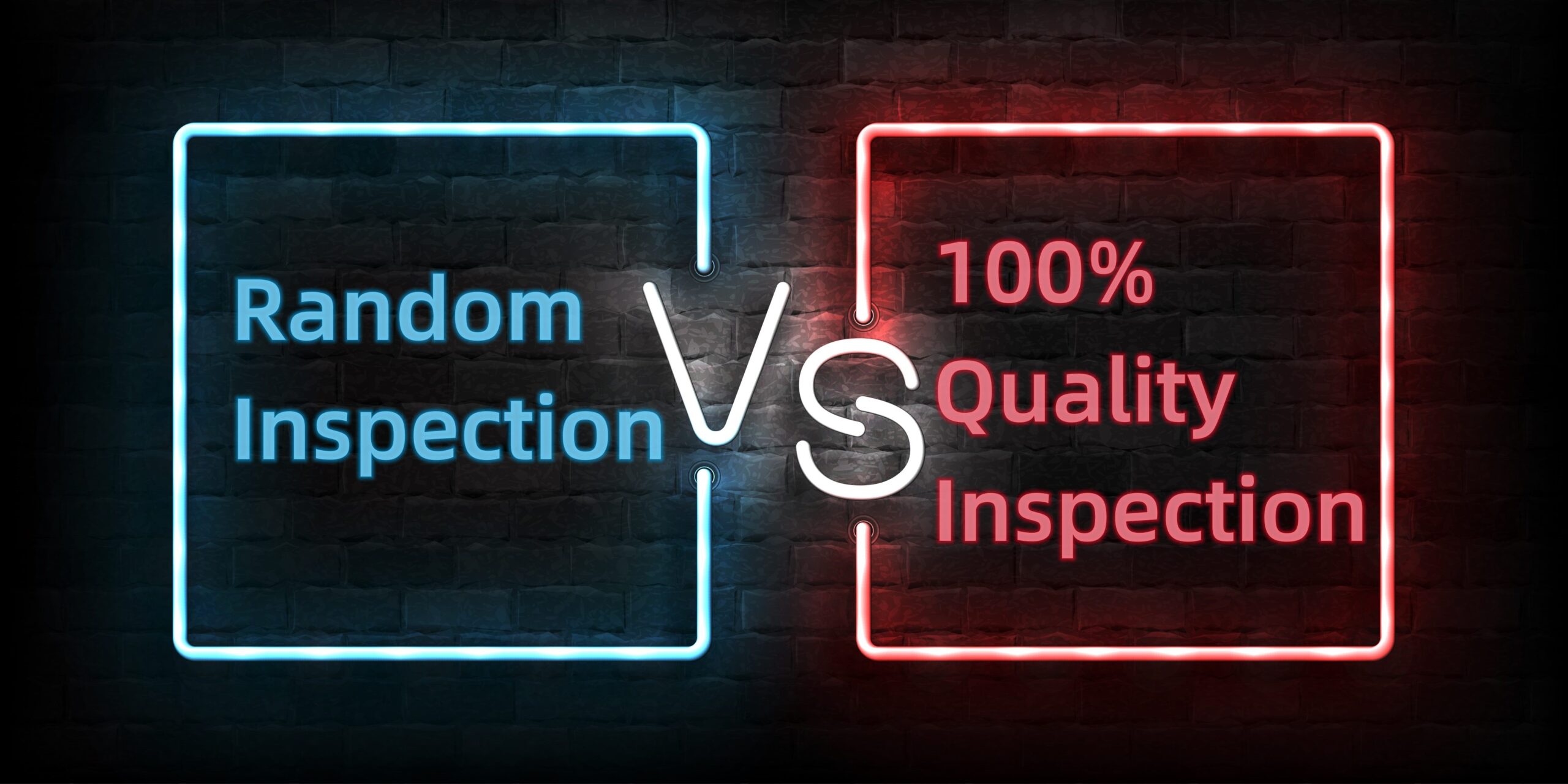
Random Quality Inspection:
Advantages:
• Checks are less expensive and less time-consuming than 100% quality inspection.
• Spot checks can be used to test a variety of types of products and processes.
• Checks are often performed by machine rather than humans, which can reduce the costs associated with manual inspections.
Disadvantages:
• Spot checks are less accurate than 100% quality inspection.
• Checks can be used to test a variety of types of products and processes, but they cannot be used to check every product or process.
100% Quality production inspection:
Advantages:
• 100% inspection is more accurate than random inspection.
• Checks can be used to test every product or process and are therefore more efficient.
Disadvantages:
• 100% inspection is more expensive than random inspection.
• Inspection can be used to test various types of products and processes, but it cannot be used to inspect each product or process.
Should 100% Quality Inspection be Finished in the Supplier’s Factory?
The answer to this question depends on your objectives. If you want to inspect an incomplete product, conducting a 100% inspection at the supplier’s factory will be more efficient and accurate.However, if you want to test products that have already been fully assembled or tested, then spot checks may be the best option.
For example, if you are purchasing electronic components for a new product line, spot checks are not enough. Because it is difficult to determine whether each component has been correctly assembled or tested.
When is a random quality inspection required?
When you have a large order and want to ensure that the supplier does not compromise product quality. At this point, a random quality inspection is required. This is especially important when dealing with low-cost suppliers, who may be tempted to cut corners in order to reduce costs. When you ask for a free sample of products before placing an order, this can also help prevent issues with quality control later on down the line.
A random quality inspection is often required by the supplier, so you should make sure that it’s included in your contract with them. This will help ensure that any issues with quality control are sorted before they become a problem.
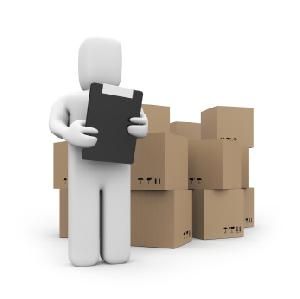
Takeaway: Random inspection and 100% quality inspection are both good, but depend on the inspection goals.